InterContinental Sydney
Value: $104m
Client: Mulpha
Architect: Woods Bagot
Completion date: September 2022
The refurbishment of the hotel has been one of the most complex and ambitious to date, calling on Built to find innovative solutions to unique challenges and achieve the strongest outcome for the client, hotel operator and guests.
The refurbishment was rolled out in five stages, beginning with a full upgrade of the building’s services, the complete refurbishment of all guest rooms, public area works on levels five and six including a new bar, restaurant plus lobby, upgrading the wellness amenities on the rooftop level and creating a new bar (open to the public for the first time), and a restoration of the building’s heritage components.
Due to the scale of the works, Built recognised this refurbishment would require unique and innovative methodologies, particularly around ensuring the hotel stayed operational.
Early Contractor Involvement (ECI) ensures we start strong and finish stronger
The project began with Built undertaking Early Contractor Involvement (ECI) in 2019 to identify and respond to the challenges presented by the job.
One of the greatest challenges of the project centred around undertaking such a major refurbishment while the hotel continued to operate and host guests with minimal disruption. Critical to this was a well-managed and precise programme of works to allow the hotel to manage bookings and have the works completed as efficiently as possible.
To support this, Built ran an extensive ECI process involving thorough investigations to plan and design all elements of the project, while also identifying any issues that could add delays and finding solutions to mitigate potential risks.
This process allowed us to demonstrate and provide accurate information to the client, allowing them to make informed and sound decisions based on detailed investigations around the building. This also allowed Built to harness relationships with key stakeholders and give insights to the best methodologies to put forward to minimise risk and mitigate impact on the hotel’s operations.
Through the ECI, Built discovered the building services including mechanical, electrical, plumbing and air conditioning, required upgrading and would need to be replaced. Through extensive planning, Built developed solutions for these services while ensuring business continuity for the hotel.
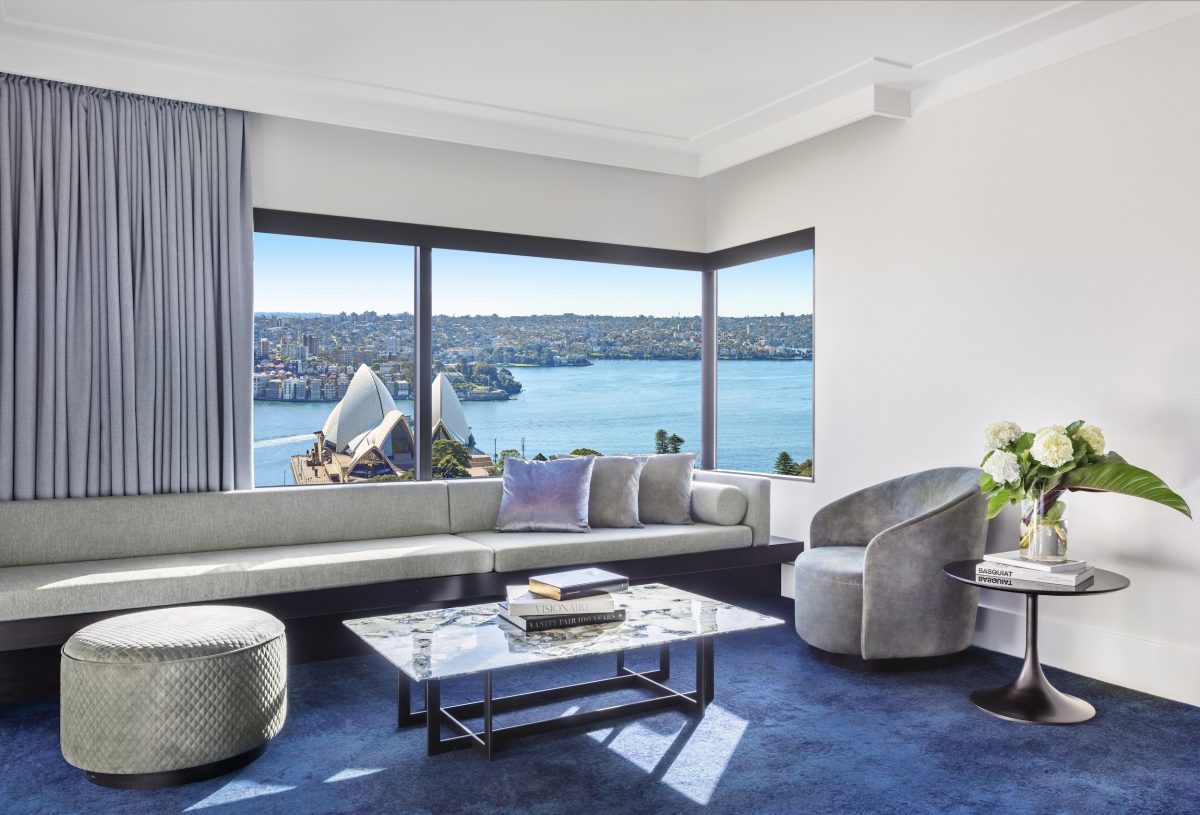
“One of the key drivers for success was that everyone was motivated for the same outcome for this project which was ultimately delivering the quality experience to the end users and handing over a building that was more efficient and easier to maintain and operate.”
John Manahan, Senior Project Manager, RCP
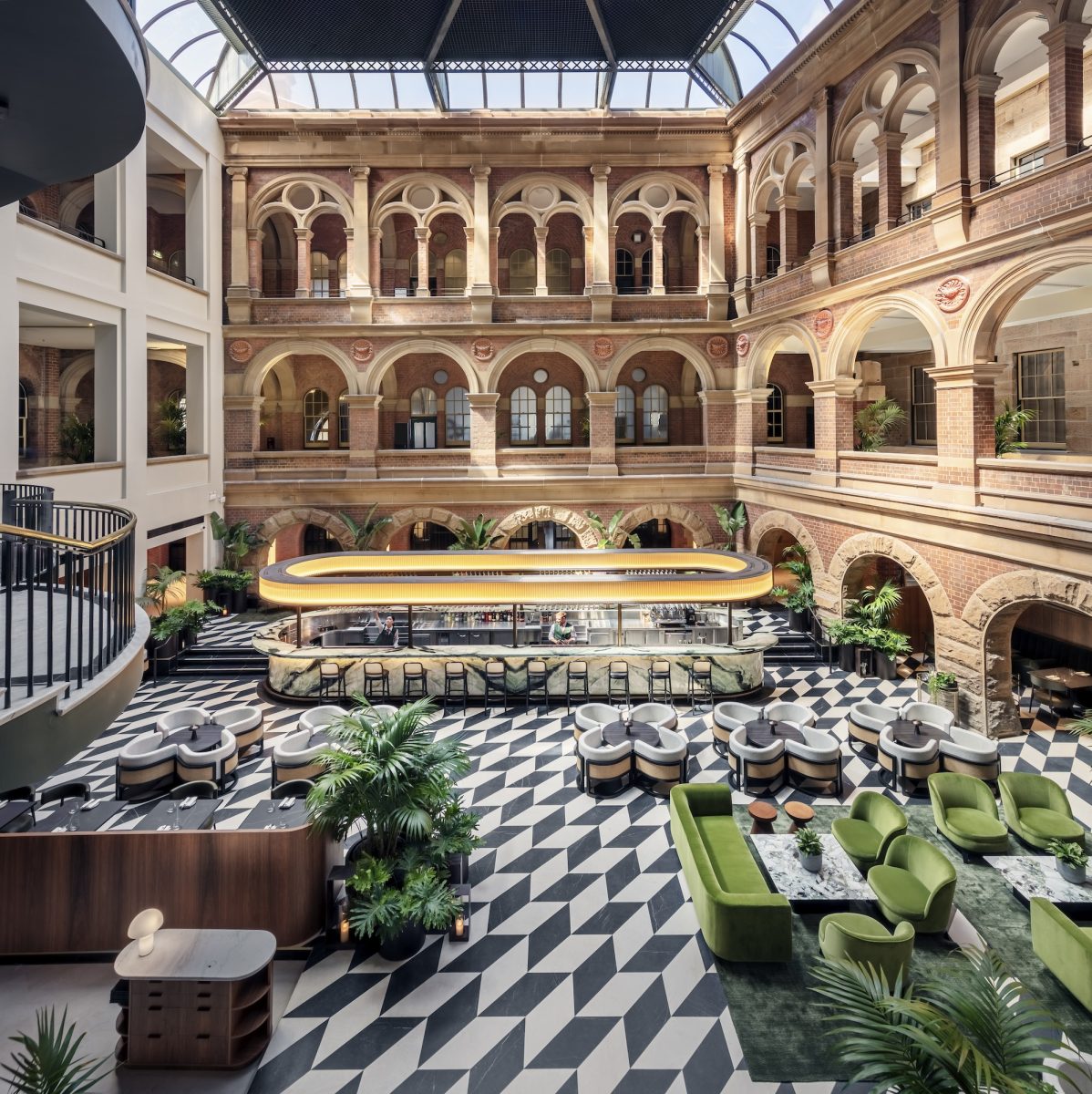
Restoring a state significant, heritage building
The 1851 Treasury Building is a state significant, heritage listed building, built from sandstone and with many original features, both inside and out. The scope involved the restoration of the external and internal sandstone façades, timber windows, internal fireplaces, stairs, and timberwork. Further to this a range of services were required to be upgraded within the heritage areas.
During our ECI the scope and extent of works was defined, a methodology developed, and staging plan established to undertake all work elements with careful consideration for safe access and protection of the heritage fabric. Working closely with the heritage consultant team, Built’s team were commended for the due care and attention to detail in cataloguing and managing the restoration.
Live environment service infrastructure replacement
Replacing major mechanical and electrical infrastructure in a live operating hotel required our team to draw on their extensive live environment refurbishment experience. Through the ECI, methodologies were developed for the change over and staging of these works to maximise business continuity.
The chilled water system reticulated through the entire building and the original system presented several issues, requiring complete rerouting. To mitigate the need of having to open every block wall through the building in order to replace pipework, Built devised a solution whereby we created an area in the back-of-house and created a new single riser which created the ability to distribute cold water reticulation pipework onto each floor, while the existing system was still operational.
Temporary chillers, cooling towers and generators were utilised at various points to enable the changeover from the existing system and the staging of the changes was planned and managed in intricate detail to ensure successful delivery.
Through the ECI the team developed a program to complete major electrical and mechanical board upgrades during a single full building shutdown. This was minimised to a four-week period during which site operated 24 hours a day to remove and replace all main switchboards and upgrade the mains cabling throughout the tower. The planning involved in de-risking this work element was significant and the effectiveness of this planning was demonstrated by the successful execution of the shutdown.
509
Guest rooms refurbished
587
Windows replaced
2022
MBA Awards Safety Innovation Award Winner
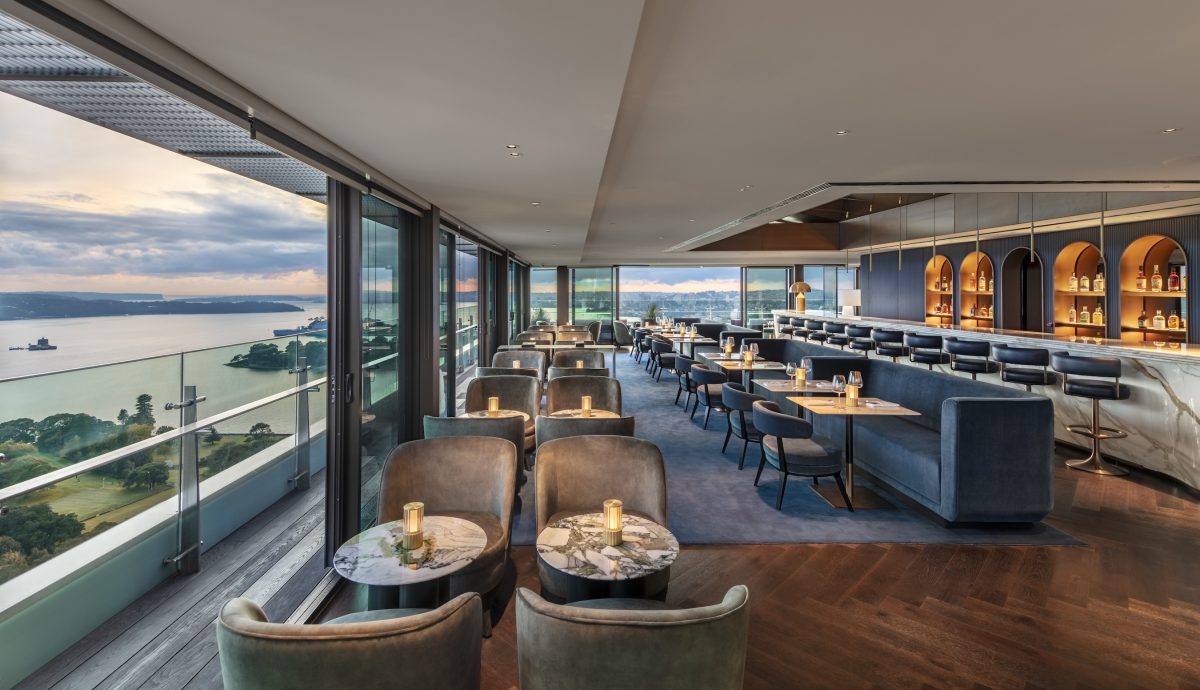
Developing smart solutions for complex problems
Following the successful upgrade of the building services, Built began refurbishing all 509 guest rooms of the hotel, including replacing the windows with full glass panels for uninterrupted harbour views. This aspect of the job was a feat within itself.
With 587 windows across the building requiring replacement, Built undertook significant planning to design a custom solution to replace the windows internally.
Initially, the window replacements were not in the scope of works because of the scale and difficulty of the job. The preliminary approach involved the placement of scaffold around the perimeter of the building, or the use of mast climbers. This would have been a cumbersome method and would have majorly impacted guests and the hotel’s operations.
Built was able to identify a methodology in the form of netting that had never been used before and which isolated our works to a single floor, mitigating our impact on guests above and below and enabling us to continue works in increment weather.
The initial stage involved designing a window that could be easily installed internally and be done in a way that is safe, fit in the lifts and could be weather sealed to the same degree as a window replaced from the outside.
Once this phase was completed, the next challenge was to measure all 587 windows externally and internally to standardise the unit sizes and ensure consistent detailing, before offshore procurement commenced.
This strategy proved to be highly effective in mitigating the potential of delays associated with rain and wind disruption and allowed the team to replace a floor of windows in eight days, without disruption to the hotel’s operations. The window replacement works required a total of 16,000 work hours during which there were no incidents or falling objects.
Built won the MBA Awards 2022 Safety Innovation Award for the window installation methodology.
“Our key starting point is to understand how the hotel operates, from how the staff use the building at the back of house and their needs for the loading docks and service lifts so that we can tailor our approach to best suit their needs. We find ways to collaborate with our client so we’re all working together to achieve the best outcome. For someone who works on hotels like myself working on an iconic property like the InterContinental in Sydney is a once in a lifetime job.”
Adam Arnold, Construction Manager, Built
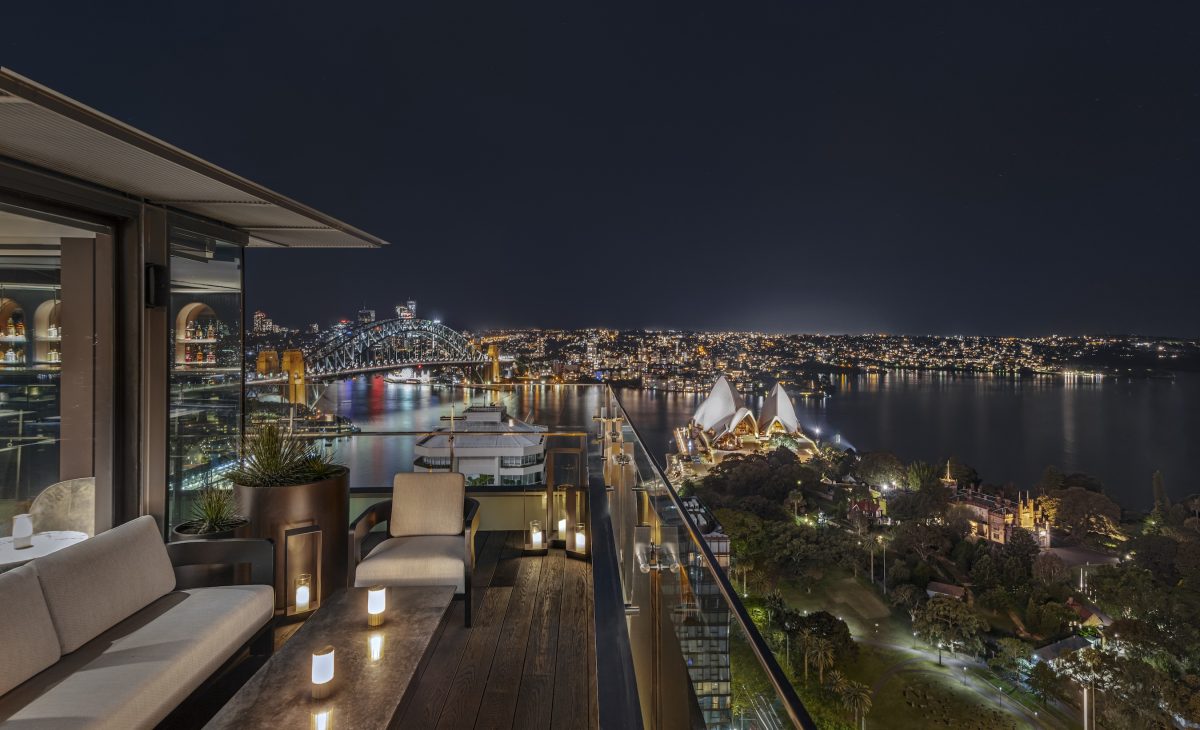
An invisible contractor delivering visible quality
Built’s ability to work as an invisible contractor on complex refurbishment projects has driven an extensive track record in luxury and high-end hotel work which has included the Park Hyatt, Hilton and Four Season’s hotels in Sydney alone.
Built’s key starting point at the InterContinental Hotel was to understand how the hotel operates, including how the staff use the building at the back-of-house, loading docks and service lifts, so that we could tailor our approach to best suit their needs.
To ensure we remained invisible, we put into place noise and vibration management plans, which included ceasing noisy works during peak times and special events, such as weddings. We also utilised just one of the three back-of-house lifts for our works, to ensure that the hotel staff were minimally affected by our materials handling.
During works in public areas, we approached the hotel section by section, ensuring that it could continue operating as usual in one area while we worked on another.
As always, we found ways to collaborate with our client so that we were all working together to achieve the best outcome while allowing the hotel to deliver top-class accommodation during works.
Clear, proactive and immediate communication is key
Built is a committed, proactive and solution driven partner for every client and we remained diligent and open from the ECI phase through to completion of this refurbishment.
We worked hard to understand the key drivers for each stakeholder and worked as a conduit, bringing together all those drivers and ensuring that every stakeholder was considered so that an optimal approach to the works could be attained.
We provided customised processes to give Mulpha oversight of the design throughout the works and we adapted solutions where necessary.
We also maintained a commitment to join daily hotel briefings and invited the hotel team to do defect walks of each guest-room level as it was completed, to ensure works were up to standard before handing over.
Over the course of the works, Built faced a number of environmental conditions that could not be avoided. COVID-19 created many complexities, as did overseas supply, supply chain and labour shortages. To embrace and overcome these challenges, Built was adaptable, flexible and patient, coming up with solutions to each problem as it presented itself.