Built delivers Perth’s first cutting-edge timber hybrid office tower
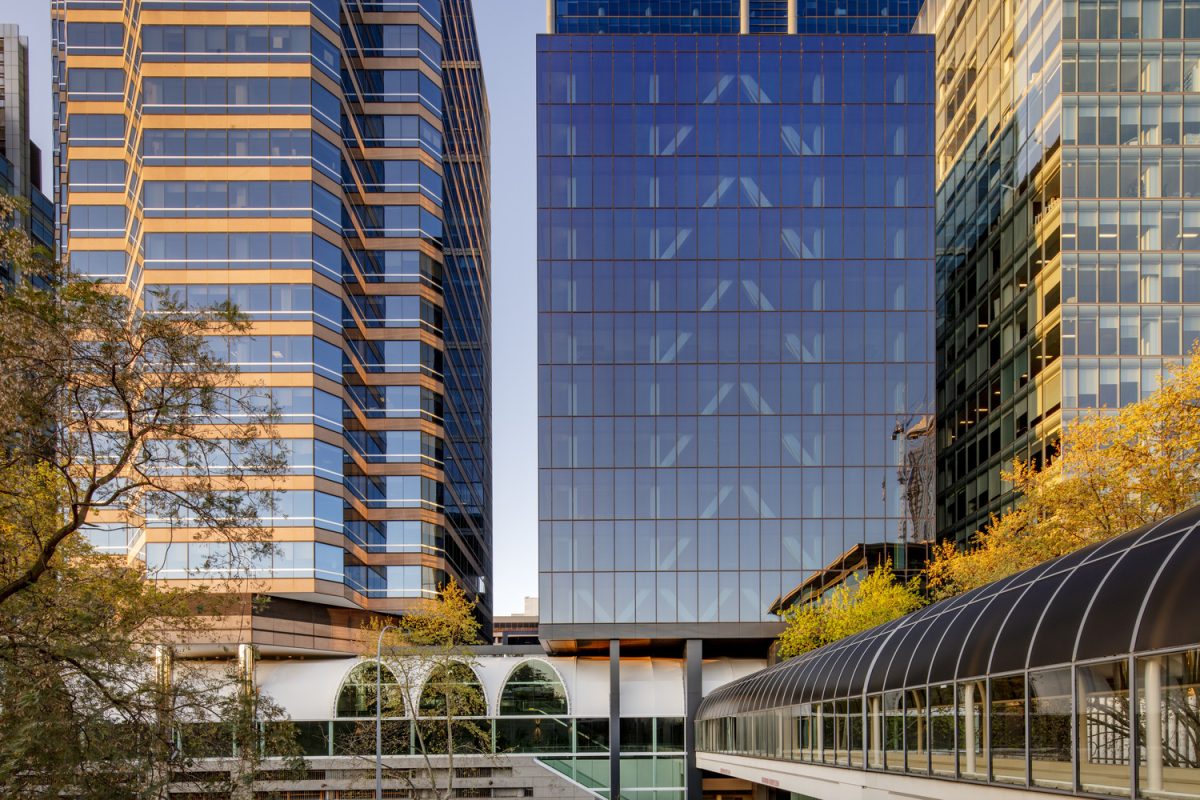
Having successfully delivered Perth’s first hybrid timber office tower, Built proudly joined GDI Property Group and Arup for the official opening of Westralia Square 2 (WS2).
Standing as the harbinger for the change in approach needed for developers and tenants to meet and deliver sustainable commercial developments into the future, WS2, developed by GDI Property, was officially opened by Deputy Premier the Honourable Rita Saffioti MLA.
“As a builder, we play a critical role in linking our clients and their sustainability aspirations and the materials that bring these to life,” said Jon Stone, Director, WA, Built.
“With an embodied carbon saving of about 70% compared to a concrete equivalent building, WS2 sets a new standard for sustainable commercial developments and exemplifies the opportunities adaptive reuse and hybrid timber construction present in reducing embodied carbon,” added Mr Stone.
GDI CEO and Managing Director, Stephen Burns, said the success of the timber hybrid build placed the issue of sustainability, particularly relating to embodied carbon and scope emissions, at the forefront of design thinking and provided a resounding solution.
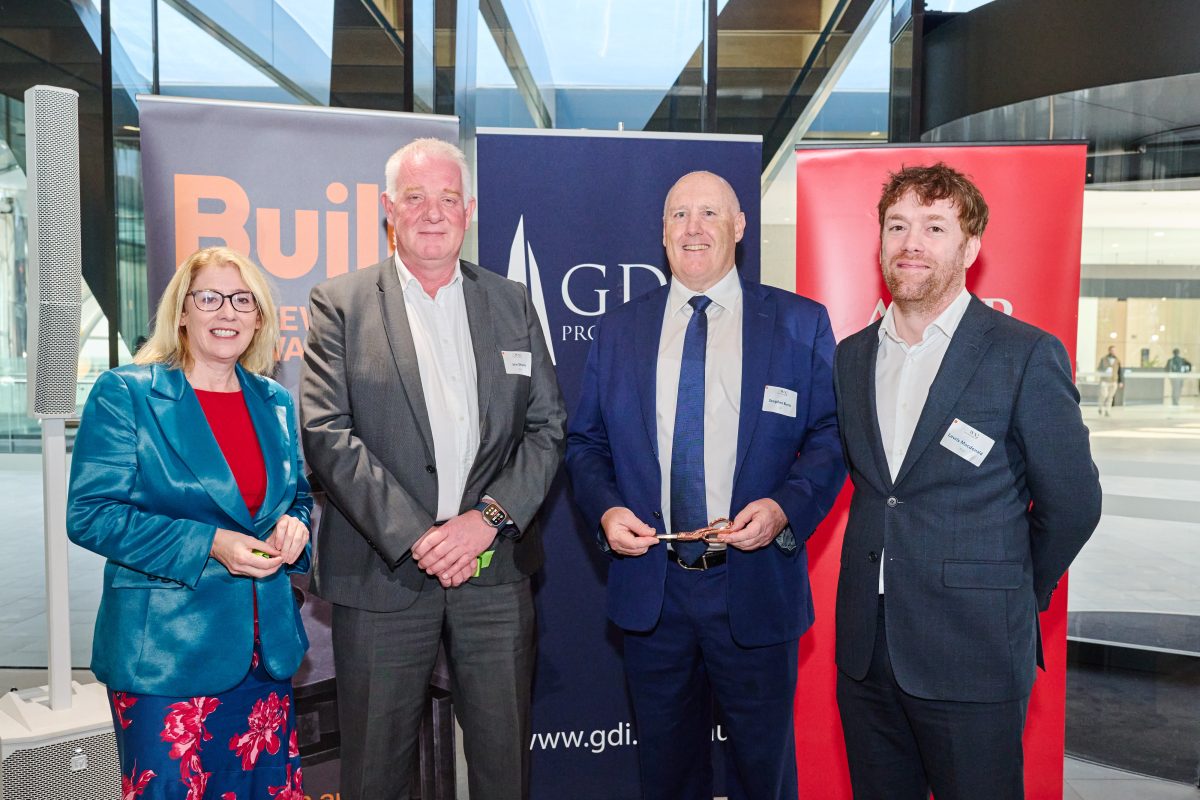
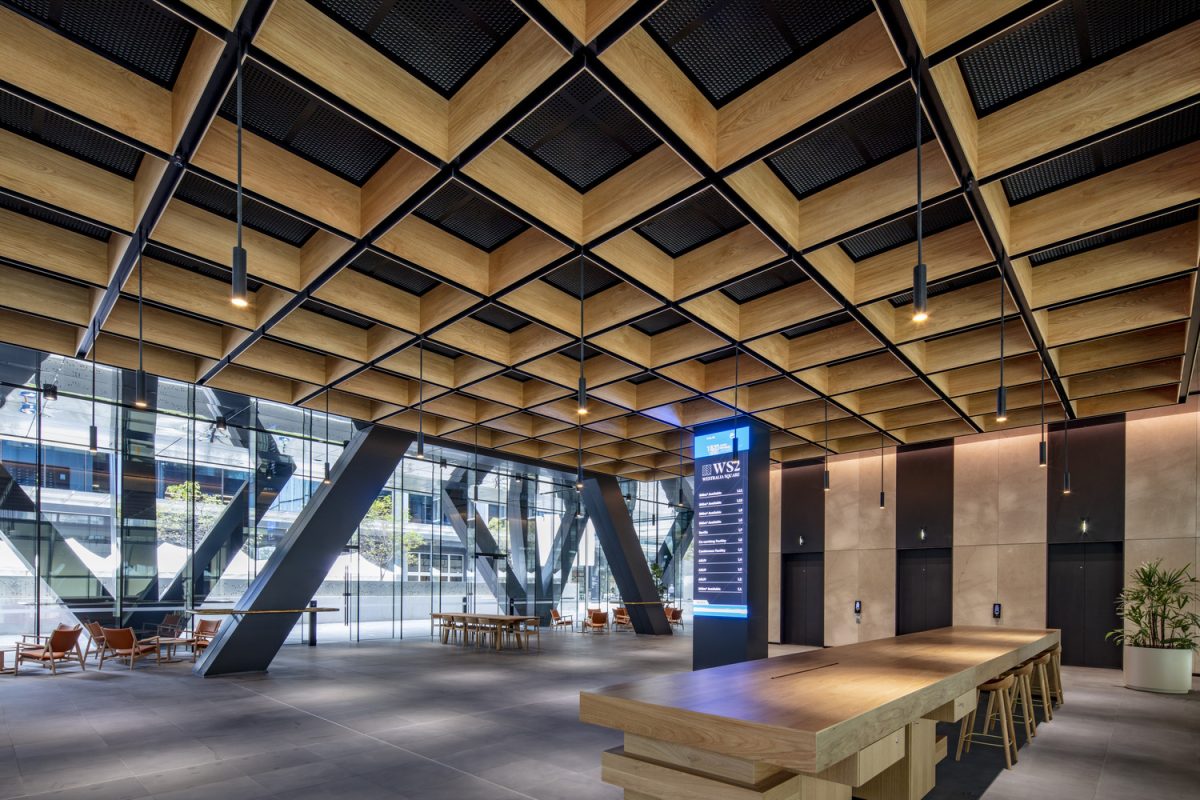
“GDI Property took the decision to develop WS2 as a timber hybrid building, a novel approach for buildings in the Perth CBD, as it delivers significant project benefits as well as a step-change in the embodied carbon results which is becoming more important for governments, industry and the broader community,” Mr Burns said.
“We are especially pleased that both Arup and Built, who were both integral partners in the creation of WS2, have recognised the intelligence and impact of WS2 and have chosen it to be their new Perth headquarters.”
In addition to setting the standard for embodied carbon reduction, WS2 demonstrates the opportunity hybrid timber construction presents to optimise project delivery.
For example, the deliberate choice of steel and timber meant that the WS2 structure and facade was built approximately 30% faster than a similar conventional concrete structure.
The removal of concrete hence elimination of back propping constraints also saw the acceleration of the internal fitout programme, six weeks earlier than a conventional concrete building.
Furthermore, with our digital-first approach to construction, including extensive experience using digital engineering, building logistical challenges and design detailing/shop drawings were resolved well ahead of start on site due to the high volume of off-site manufacture.
The Built team could not only ensure a high level of quality control was achieved on the project but also reduce the risk of rework onsite.